ISO 9001 Certified
Oil Solvent Extraction Technique
Solvent extraction is one of the most advanced oil extraction technologies. It has been continuously improved and perfected since its introduction in 1870, and so far, it's the main way to make vegetable oil in the world's oil industry. In this section, we will learn detailed knowledge on this technique.
Ultimate Guide to Solvent Extraction
The solvent extraction method includes direct extraction and pre-pressing extraction.
In oil solvent extraction, the principle is: use solvents that dissolve oil and grease, through wetting, penetration, molecular diffusion and convection diffusion, so that grease in embryos can be extracted.
The process includes: Pretreatment, solvent extraction, wet meal desolventization,miscella oil evaporation and stripping, solvent recovery,etc.
Factors affecting oil extraction:
The nature of the material embryo and pre-pressed cake: The sturcture and moisture of the embryo
Extraction temperature: about 5℃ below the initial boiling point of the solvent distillation process
Extraction time: “economic time”; generally 90-120 min.
Height of the material layer: try to increase the height of the material layer
The effect on solvent ratio and miscella oil concentration: 0.8 ~ 1:1, 18 ~ 25%
Drainage time and the amount of solvent contained in wet meal: 15~25 min, 25~30% of solubility
Detailed process flow:
Oil and grease leaching process:
Oil extraction method: immersion type, spraying type, mixed type three.
Extractor species: Tank in series, Crawler type(Spraying type), Rotocel, Loop(mixed type)
Wet meal desolvation and drying (Wet meal toasting) process:
Manufacturing method: indirect steam heating combined with direct steam negative pressure stirring.
Requirements: Moisture in the meal≤8-9%, solvent residue in the meal≤0.07%. Discharged meal tempearture: >105℃ or ≤70-80℃。
Desolvation and drying process
Toasting and drying equipment: Common seen is DT-type Desolventizer
Miscella oil evaporation and stripping process
Process: Miscella oil filtration-Miscella oil storage tank–First evaporator–Second evaporator-Stripping tower–Extracted crude oil
Miscella oil evaporation: Utilize the different boiling point of oil and solvent, heat the miscella oil up to boiling point temperature, make the solvent evaporation and separate from the oil. Miscella oil outlet tempearture in the evaporator shall not exceed 110℃,concentration90-95%.
Miscella oil stripping: Means miscella oil vapor distillation.using distillation method, make the boiling point of higher concentration miscella oil reduce, thus the less solvent ratio in the miscella oil can be stripped out fully. The solvent residue in the crude oil index:50-500ppm.
Solvent recovery process
Through desolventization and miscella oil evaporation process, collect the non-condensed solvent gas. Main equipment: Condenser,Water separator,Cook tank and Non-condensed gas recovery device,etc.
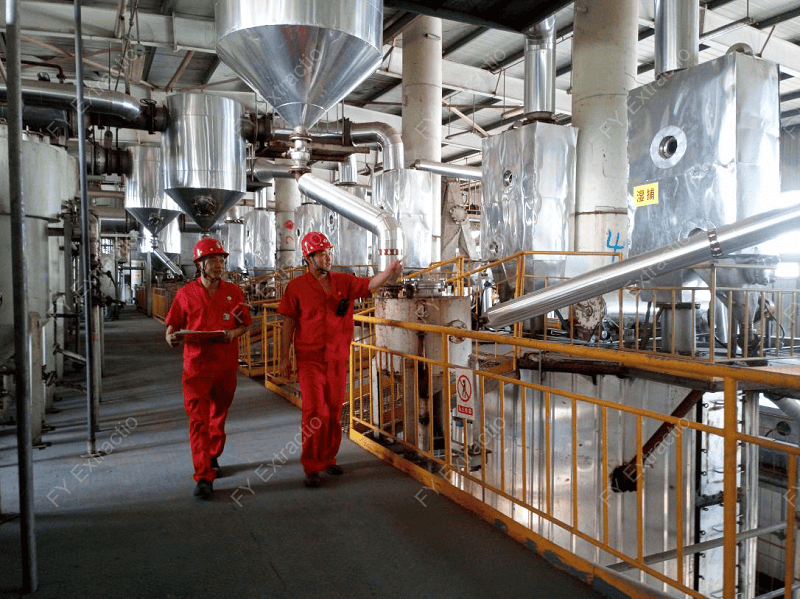
Explore FY Extractio's Solution
Solvent Extraction Glossary
Solvent
An organic substance capable of dissolving grease in any proportion, fully and rapidly.
Industry n-hexane
It is mainly composed of hexane and has a distillation range of 67℃~71℃. It is mainly obtained by the distillation and separation from the residual oil of Platinum reforming . It is used as a solvent especially for the extraction of edible vegetable oils.
solvent extraction
Also called “extraction”. The process of extracting oils and fats from oilseeds with organic solvents.
solvent ratio
The weight ratio of the extracted material to the solvent per unit of time.
percolation extraction
A method of extracting solvent by spraying it in contact with a material.
immersion extraction
A method of material immersing in the solvent.
direct extraction
The process of extracting oil directly from the oil material after pretreatment.
pre-pressing extraction
The process of leaching the higher oil content cake after the oil is partially extracted by pre-pressing.
extraction temperature
In the extraction process, the temperature conditions set according to the solvent distillation range and leaching process.
extraction time
The time period from extraction start to meal discharge.
permeability
Extraction process, the degree of solvent penetration into the internal pores of the material through the material layer.
countercurrent percolation extraction
During the solvent extraction process, the sprayed miscella oil concentration is reduced along with oil content reducing in the material. Finally adopts fresh solvent to spray.
extracted oil
Oil extracted from material or pre-pressed cake by using certain organic solvents, such as industrial hexane, etc., to dissolve the oil.
forbidden zone for solvent extraction
A zone defined at a certain distance around the extraction plant, including the necessary ancillary buildings, in order to ensure the safe operation of the extraction production. It is forbidden to enter or otherwise work with people not directly related to the extraction process.
meal discharging
The process of discharging the extracted meal from the extraction tank after extraction.
miscella treatment
The process of purifying the oil mixture, removing impurities, and separating the oil from the solvent.
miscella
A mixture of oil and solvent.
miscella concentration
The weight percentage of grease in the total oil mixture.
miscella pre-heating
The process of heating a blend of oils to a temperature at or near the boiling point of the blend before evaporation.
miscella evaporation
Since the solvent is volatile in the miscella oil, adopts heating method to make solvent vaporization then concentrate the miscella oil out.
miscella stripping
A process that basically removes a small amount of solvent from a concentrated miscella oil by using the principle of steam distillation.
Normal pressure evaporation
The process of evaporation of mixed oil under normal pressure.
negative pressure evaporation
The process of evaporation of mixed oil under negative pressure using vacuum equipment.
meal treatment
The process of drying the wet meal discharged from the extractor to remove as much solvent as possible and to make the temperature and moisture of the meal suitable for storage.
extracting meal
Normally oil residue in the meal is around 1%, moisture is under 12%, the solvent residue is under 700mg/kg. Divides high temperature and low teperature meal according to different desolventization temperature. It is widely used in food industry and animal feed industry.
high temperature desolventized meal
The desolventized meal product after the material is extracted and desolventized according to the common desolventizing process, the desolventizing temperature can reach 105 ℃.
low temperature desolventized meal
The meal product after the billet is desolventized by the low temperature desolventizing process after extraction, and the desolventizing temperature is generally not more than 80 ℃.
wet meal
The meal containing solvent after leaching.
solvent content in wet meal
The content of solvent in wet meal.
Meal&fines separation
The process separate the fines which is taken by the mixed steam toasted from the desolventizer.
low temperature desolventizing
The desolventizing process in which the meal temperature is lower than 80℃.
solvent recovery
The process of solvent recovery from the desolventizer, miscella oil evaporation and stripping process.
mixed vapour
A mixture of solvent vapor and water vapor.
water separation
The process of recovering solvent from waste water by separating solvent and water through sedimentation, taking advantage of the solvent’s insolubility in water and its lower specific gravity than water. The water separation equipment in this application is called a water separator.
waste-water boiling
The wastewater discharged from a water distributor is heated and boiled to recover trace amounts of solvents. In case of improper operation of the manifold, when the wastewater containing more solvents is discharged in a milky color, the wastewater should be sent to boiling to recover the solvents. The equipment used in this application is called a wastewater boiling tank.
solvent-carrying air
The uncondensed gas in the leaching system.
exhaust gas/vent gas
The uncondensed gas from the final condenser.
solvent recovery from vent gas
The process of recovering solvent from vent gas.
lean oil
Mineral oil used to absorb solvent.
rich oil
Mineral oil that has absorbed solvent vapors.
waste gas
A gas that is exhausted to the atmosphere after the solvent has been absorbed or adsorbed in the exhaust gas.